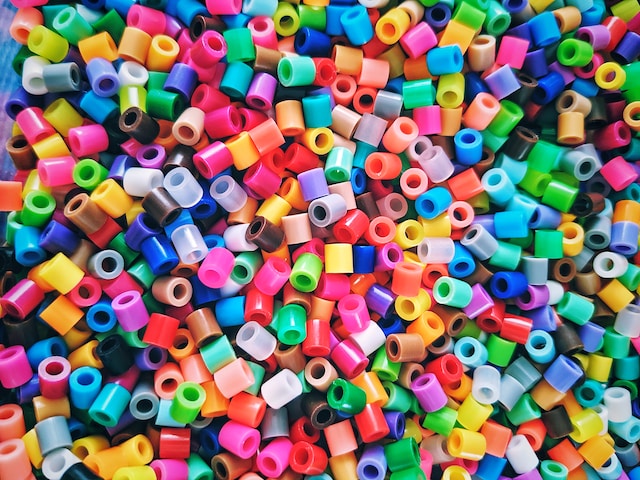
Features of CNC Machining for Injection Molds
Injection molding is an assembling procedure that can make intricate parts. It can include features such as bosses, ribs, and metal inserts. It can also add side cores and holes.
Injection molding takes a bit of time to create the mold, but this pays off through high-volume production.
Precision
Injection molding allows designers to create a wide variety of plastic products. The injection process uses high-pressure injectors to force molten plastic into the mold cavities. The resulting part is then ejected from the mold using ejector pins or a robotic arm. Some of these parts are made from polytetrafluoroethylene (PTFE), a highly versatile chemical-, light-, temperature-, water-, fatigue-, and corrosion-resistant type of plastic.
Compared to injection molding, CNC machining can create better tolerances at a lower cost. The machine works according to a computer program rather than an operator’s manual.
Another advantage of CNC machining for injection molds is its versatility. It can be used for several tasks, including creating melting barrels and cauldrons that melt raw materials for injection molding. In addition, CNC machines can fashion nozzles to direct the melted material into the molding crates. The precision of these metallic parts is critical to the success of injection molding.
Speed
Injection molding is a popular method of manufacturing plastic parts. It is used in various applications, including automotive components, storage containers, and furniture. This process uses an injection mold to form a plastic part from molten material that is then solidified into its final shape. The intent, function, and lifespan of the final product are essential factors to consider when designing for manufacturability.
CNC machining and injection molding are two production processes that create parts using highly different methods. Injection molding is a rapid, high-volume manufacturing technique that uses expensive steel and aluminum molds to produce parts.
Injection molding can produce many parts per base machine, and multiple-cavity molds allow for fast turnaround times. However, it is challenging to accommodate design changes in injection-molded plastic products. Plastics expand and contract at different rates, causing non-uniform pressure-induced deformations and dimensional deviations. Thermoforming, on the other hand, is a more flexible and cost-effective alternative to injection molding.
Repeatability
Injection molding is an expansive manufacturing technique that involves making the same part in large volumes. This allows for a high level of consistency and accuracy in production. However, this process is only suitable for some parts and may result in cosmetic imperfections. These blemishes include parting lines, gate marks, and ejector pin divots. Fortunately, these defects can be cured with machining.
CNC machining is also a good choice for injection molds with complex shapes that require sharp internal corners. These features are difficult to achieve with injection molding, especially when the product design is expected to change often.
Another benefit of CNC machining is that it is compatible with many materials. This makes it ideal for shops that prioritize precision over quantity. Injection molding, on the other hand, is primarily used with thermoplastics. These are polymer resins designed to soften or liquify when heated. Other softer materials, such as elastomers, polytetrafluoroethylene (PTFE), and metals, cannot be injected into a caret mold.
Cost
Injection molding uses a process that melts and injects plastic into a mold under high pressure. The process is a fast and inexpensive way to produce parts for various commercial and industrial purposes.
Complex part designs can add significant costs to injection molding production. These costs can be related to the complexity of the part’s side A and side B designs. Side A is the cosmetic side of a part expected to be smooth and aesthetically pleasing, while Side B contains the hidden structures that support the part’s usage.
CNC machining can work with an extensive range of materials, but some softer materials may need more precision during the milling process. Some more delicate materials may require additional finishing services such as annealing, sandblasting, and powder coating to ensure the part’s durability and aesthetic appeal.